butcher__51 tweetje adta.
Már nem emlékszem, hol hallottam először az asszonyfaktor szakszót. Aki hozzám hasonlóan geek, annak ezt nem kell túlmagyarázni: adott vágyaink tárgya, az épp aktuális gadget, ami sajnos mindig pénzbe kerül. A gadgetre költendő pénzt a párjaink elsöprő többsége szerint értelemszerűen egy csomó hasznosabb / értelmesebb / et cetera dologra kellene elkölteni az újabb sz@r kütyü helyett.
Talán csak egy olyan csajt ismerek, akinek tágabbra nyílik a pupillája ha megtudja, hogy mondjuk kijött egy új stabil kernel, ráadásul ő valahol tőlem már jó messze ugrál ki mindenféle repülőkből.
Egy szó, mint száz, az asszonyfaktor a partnerünk kütyüvásárlási engedékenységi koefficiense. Mivel ez az esetek nagy többségében a nulla felé konvergál, próbáljunk meg némi analízissel javítani a helyzeten, hátha lehetséges!
Tegyük fel, hogy vágyaink tárgya egy 3D printer. Sajna a printerünk nem szép (legalábbis a női szemnek biztosan nem), nem lesz tőle simább a bőrünk, nem is igazán öltöztet. Valamit azonban mégis tud, amit a többi gadget nem: gyártani! Ha tehát abból indulunk ki, hogy az imádott nőnek olyan tárgyakat készíthetünk, amelyeknek ő is örül || hasznát veszi, akkor esetleg némi növekedésre tudjuk így bírni a fent emlegetett együtthatót. Nézzünk példákat.
A háztartás körül sok olyan apró defekt létezik, amire viszonylag egyszerűen készíthetünk fixet.
Lehet ez egy egyszerű fogkefetartó:
vagy egy gyűrű a partvisnak, hogy ne a sarokban álljon:
vagy akár egy custom méretű kis polc:
Természetesen lehetünk ettől sokkal advancedebbek is. Ha körbenézünk a Thingiverse-en, ott rengeteg ötlet várja, hogy bevessük!
Vázák:
Szappanadagoló:
Sütiformák:
Muslincacsapda:
…és még órákon át lehetne sorolni. Lehet folytatni az indoklást otthoni meghibásodott eszközök könnyű és olcsó javíthatóságával – mondjuk egy frissen eltört fogaskerékkel a mosogatógépben, amely a gyártótól rendelve sokezer HUF-os tétel, mi azonban örömmel legyártjuk, fillérekből. Bármi, ami műanyaggal pótolható és belefér a 20x20x20 centis dobozunkba, azt mi bizony nagy lelkesen állítjuk elő – és ezzel nem is füllentünk sokat, hisz a szemünk egy idő után automatikusan “mit hackeljek ma?” üzemmódba kapcsol majd.
A mai posztot andreas által tervezett izé, Béluka zárja, köszönjetek neki szépen:
Holnap hardverezünk egy kicsit, stay tuned!]]>
Monthly Archives: November 2012
3D nyomtatás – tervezzünk, de mivel?
AutoDesk Inventor / SolidWorks méretű vadállatok funkcióit ismertető demo videókba, akkor egy ideig még sajnálva néztem a szépen összegyűjtött sok-sok infot a posztban, aztán nyomtam egy ⌘A-t, majd az egészet kidobtam a kukába. Hogy miért? Mert egy fogkefetartó legyártásához nem fogunk 5000 EUR-t elkölteni. Ahelyett tehát, hogy egy átfogó CAD/CAM szoftver képet festenénk, nézzünk meg inkább négyféle alkalmazást, amivel kacérkodom.
Google Sketchup
A SketchUp ingyenes mezei és 495 USD-ért mért Pro változatban létezik, Windows/Mac OS X alatt. Elsősorban arra fejlesztették, hogy a népek a Google Maps-hez legyártsák az IRL épületeket, szép vektoros formában, de azért *.3d objketumot is építhetsz vele. Az ingyenes verzió ugyan nem képes .STL formátumba exportálni, de a Cura tud a SketchUp által produkált .DAE formátumból olvasni, úgyhogy ez a probléma nem probléma. A Google SketchUp volt az első, ahol a push/pull elvű modellezést láttam, nagy vehemenciával neki is indultam anno, hogy majd legyártom a saját házunkat benne, így tanulva meg az eszköz használatát. Elég sokat kínlódtam vele és úgy tűnt, hogy a push/pull modellezés során előállt felületek nem mindig illeszkedtek precízen egymáshoz. Én anno a 7-es verzióval kísérleteztem, azonban azóta van 8.0. A nyolcasban megjelentek a 7-ben még nem létező solid boolean toolok, ami objektum tervezésnél nem jön kifejezetten rosszul. Íme a what’s new video kedvcsinálónak:PunchCAD ViaCAD 2D3D
A PunchCAD nevű gyártó háromféle consumer kategóriás CAD alkalmazást kínál a kétféle, professzionális felhasználásra szánt szoftvere mellett Windowsra és Mac OS X-re. Ebből a Mac App Store-ba is listázott ViaCAD 2D3D a maga 100 USD-s árával még a megfizethető CAD kategória. Én ebben gyártom a sok reciklálandó plasztikot egy ideje. Két dolog nem tetszik benne: az egyik, hogy a push/pull tool nem mindig talál rá az extrudálható face-ekre (ugyanakkor egy másik extruder tool ugyanazt a területet simán kinyomja), a másik pedig a gyenge help. Ettől függetlenül 100 USD-t megér. Nézzünk meg az előző, 7-es verzióból egy rövid demot:ThinkerCAD
WebGL bázison, böngészőben futó CAD, tegnap találtam a nagy kutatásban. Nagyon guszta, elég intuitív, kicsit kevés funkcionalitással. Ebben pl. nem tudunk 2D keresztmetszetet rajzolni és azt 3D-be extrudálni és a custom alakú testek egymással booleankodását sem találtam elsőre sehol, mindössze téglatest, henger és tojás (#WTF?) alakú lyukfúrók vannak benne. Gyári nyúlfület bezzeg azonnal tud.
OpenSCAD
A végére hagytam az új felfedezettet, amitől minden coder arcnak azonnal beindul a nyálelválasztása. Az OpenSCAD ingyen van, cross-platform, és ami a legszebb: ez lényegében egy CAD scriptet olvasó compiler és mint ilyen, nyilván paraméterezhető is! Summa summarum, alkotni ebben is kell, sőt, ezt meg kell tanulni, hogy megint előjöjjön az emberben a matek. Ha valami hiányzott eddig az összes próbált alkalmazásban, akkor az a paraméterezhetőség. A lehető legegyszerűbben meg akarom egy darab szám megváltoztatásával mondani, hogy a furatok ne 3, hanem 4 mm-esek legyenek – és erre az OpenSCAD perfekt. Nézzük is meg befejezésnek danielkschneider paraméteres duplo scriptjét, miközben agyalunk a lehetőségeken://the duplo itself // parameters are: // width: 1 =standard 4x4 duplo with. // length: 1= standard 4x4 duplo length // height: 1= minimal duplo height // nibbles: true or false duplo(1,2,1.5,false); module duplo(width,length,height,nibbles) { //size definitions ns = 8.4; //nibble start offset no = 6.53; //nibbleoffset nbo = 16; // nibble bottom offset duplowidth = 31.66; duplolength=31.66; duploheight=9.6; duplowall = 1.55; //the cube difference() { cube([width*duplowidth,length*duplolength,height*duploheight],true); translate([0,0,-duplowall]) cube([width*duplowidth - 2*duplowall,length*duplolength-2*duplowall,height*duploheight],true); } //nibbles on top if (nibbles) { for(j=[1:length]) { for (i = [1:width]) { translate([i*ns+(i-1)*no,j*ns+(j-1)*no,6.9+(height-1)*duploheight/2]) duplonibble(); translate([i*-ns+(i-1)*-no,j*ns+(j-1)*no,6.9+(height-1)*duploheight/2]) duplonibble(); translate([i*ns+(i-1)*no,j*-ns+(j-1)*-no,6.9+(height-1)*duploheight/2]) duplonibble(); translate([i*-ns+(i-1)*-no,j*-ns+(j-1)*-no,6.9+(height-1)*duploheight/2]) duplonibble(); } } } //nibble bottom for(j=[1:length]) { for (i = [1:width]) { translate([(i-1)*nbo,(j-1)*nbo,0]) duplobottomnibble(height*duploheight); translate([(i-1)*-nbo,(j-1)*-nbo,0]) duplobottomnibble(height*duploheight); translate([(i-1)*-nbo,(j-1)*nbo,0]) duplobottomnibble(height*duploheight); translate([(i-1)*nbo,(j-1)*-nbo,0]) duplobottomnibble(height*duploheight); } } //little walls inside difference() { union() { for(j=[1:length]) { for (i = [1:width]) { translate([0,j*ns+(j-1)*no,0 ]) cube([width*duplowidth,1.35,height*duploheight],true); translate([0,j*-ns+(j-1)*-no,0 ]) cube([width*duplowidth,1.35,height*duploheight],true); translate([i*ns+(i-1)*no,0,0 ]) cube([1.35,length*duplolength,,height*duploheight],true); translate([i*-ns+(i-1)*-no,0,0 ]) cube([1.35,length*duplolength,height*duploheight],true); } } } cube([width*duplowidth - 4*duplowall,length*duplolength-4*duplowall,height*duploheight+2],true); } } module duplonibble() { difference() { cylinder(r=4.7,h=4.5,center=true,$fs = 0.01); cylinder(r=3.4,h=5.5,center=true,$fs = 0.01); } } module duplobottomnibble(height) { difference() { cylinder(r=6.6,h=height,center=true,$fs = 0.01); cylinder(r=5.3,h=height+1,center=true,$fs = 0.01); } }
3D nyomtatás – iPhone 5 tripod mount



3D nyomtatás – csavaring
Ez eddig rendben is van, gyártsunk akkor belőle valódi tárgyat:
A koca tervező azért azzal csak nem számol elsőre, hogy a 10 mm-es műanyagcsavar a 10 mm-es műanyagmenetben nem kicsit fog szorulni:
Ellenben ha apuci átmérőjét 1 mm-rel csökkentjük, az már jótékonyan hat a csatlakozásra:
Persze vannak okos modellező alkalmazások, amelyek ezeket a toleranciákat valószínűleg maguktól képesek okosan kezelni, de a 100 USD-be kerülő ViaCAD 2D3D v8 nem kínál nekünk ilyet. Sebaj, cserébe ma is tanultunk valamit.]]>
Film: Skyfall
Skyfall Summary: Minden perce izgalmas, komodói varánuszos, kevés lamúros, kicsit látványos grafikával hackelő hülyegyerekes, de azért nagyon kemény James Bondos. Imádtam. Értékelés: ★★★★★ ]]>
3D nyomtatás – BMW e46 mágneses tablet mount
neodímiumból, pontosabban annak vas-bór ötvözetéből (Nd2Fe14B) készül. A neodímimuról az átlagember talán annyit tud, hogy abból jó sok van Kínának, Nd a vegyjele és 60 a tömegszáma rendszáma. De ez nem az érdekes adatok mese, úgyhogy ezzel most nem is kell tovább foglalkozni, irány a 3d print meló!
Nézzük először a célterületet, ahova a tabletet szánom:
A szellőzőrostélyok alatt vagy egy horony, abba kellene beleapplikálnom. A rés keresztmetszetéről kellene tehát egy minta: ehhez vagy nekiállok hosszában kettévágni egy nagyobb flexszel ezt a részt, vagy… fogok egy darab gyurmát és belemasszírozom, hátha abból is látszani fog a rés alakja. Némi fontolgatás után ez utóbbi lett végül:
Ezt a gyurmametszetet előbb körberajzoltam:
…aztán rájöttem, hogy mekkora barom vagyok: a rég használt 3D modellezőkhöz hasonlóan valószínűleg a CAD szoftver is hagyja, hogy egy rétegre betöltsek valami segédimage-et. Így is lett:
Oké, megvan a rést kitöltő modell keresztmemszete, nyomtassunk belőle egy vékonyka lapot és próbáljuk a helyére:
Egyrészt kicsit benyúlhatna abba a fránya résbe hosszabban, másrészt nem úgy néz ki, mintha megfelelő lenne a szög. Ha a fotóra húzunk két vonalat, rögtön látszik a bibi:
A modell tabletet tartó síkja egyszerűen túl meredek és így az iPad bele fog ütközni a műszerfalba. A mádosik piros vonal mutatja a korrekt dőlést. Ebből a tapasztalatból lett aztán ez a draft:
Ezt leellenőrizzük valami ráfektetett sík darabbal is, hogy ne csak szemre legyen OK:
Jó lesz. Megvan a számunkra megfelelő keresztmetszet, most jön az, hogy az objektum belsejébe terveznünk kell egy üreget, ahova a mágnesek becsúsznak:
A fenti fotón látható példa 10x10x4 mm-es mágnesekhez készült, ám végül én ezek helyett 5 darab 10x8x30 mm-es mágnest használtam, hogy akkor is biztosan tartson a keskeny csík, amikor satura kell fékezni az autót.
A végeredmény brutális: a tabletet szinte csak csúsztatva lehet leszedni az őt tartó mágnesekről:
Ha szükséged lenne a modellre, megtalálod a Thingiverse-en.
Hétfőig messze vagyok a billentyűzettől, de utána könyörtelenül jön a következő rész, szóval stay tuned!
Update: bár a Thingiverse linken ott van, innen mégis kimaradt, hogy a mountot a kocsihoz egy darab 3M VHB kétoldalas ragasztó tapasztja oda. Ha a Burj Dubai üvegtábláit megtartja, akkor szerintem ide is megfelel majd :)]]>
3D nyomtatás – iPhone 5 autós dokkoló
Dension Gateway Lite adapter van beépítve már régóta. Ez egy iPod/iPhone/iPad illesztés a kocsi audiorendszeréhez. Az autó gyári hangrendszere CD váltónak látja az eszközt, így szólaltatva meg az arról érkező hangot. A Dension cucc átveszi az uralmat a kocsi kormányára épített audio vezérlő gombok (track forward és reverse) felett, így a kormányról léptethetem a Dension gateway-re dugott i* eszközön a lejátszási listát.
A Dension kütyüből egy régóta standard 30 tűs Apple dokk csatlakozó áll ki – ezt én egy Brodit autós dokkolóba csatlakoztatva használtam: a telefont tartja a dokkoló, a Dension felől érkező drót pedig tölti a készüléket, plusz rögtön össze is kapcsolja az autó audio rendszerével. Ez közel Nirvana volt – egészen 2012 október végéig.
Ekkor ugyanis gondolt egyet az Apple és lecserélte a 30 tűs dokk csatit egy kisebbre, megborítva ezzel a fenti megoldást. Hála az égnek kiadtak egy 30 tűs konnektor → új Lightning konnektor konvertert, amely egyrészt patent módon illeszkedik a Dension kábel végére, másrészt a Dension eszközt az átalakítóval a telefonra csatlakoztatva az audio illesztés változatlanul megmaradt. Ez szuper, már csak az új telefonnak kellene új dokkot találni – és itt jön rögtön a 3D nyomtatás.
A Brodit tartó ügyesen összerakott szerkezet. A dokk felfüggesztéséhez ugyanazt a mechanikus megoldást használják, amit a legtöbb GPS gyártója – egy forgatható talpra csavarozódik fel a dokkoló:
A telefont a dokkban tartó oldalsó támasztékok egy okos csúszkás megoldással rögzíthetőek, ami lehetővé teszi, hogy tokban levő készülékek is elférjenek az így kialakított állítható sínben.
A feladat tehát csupán annyi, hogy
- ki kell találni egy tokot a régi kábel + az új konverter számára
- elő kell állítani a régi dokk furatos talpának pontos mását
- a két komponenst “össze kell hegeszteni” a modellen
- ki kell nyomtatni a végeredményt












3D nyomtatás – alapanyagok
FFF, azaz fused filament fabrication, az eljárásé pedig FDM, azaz fused deposition modelling) az esetek nagy többségében egységes kereszmetszetre húzott/nyomott, hőre olvadó műanyagszállal etetik – zömmel 1.75 vagy 3 (=2.89) mm átmérőjű PLA vagy ABS szálat használ erre az ipar.
Mese a lebomló műanyagról
A PLA (PoliLactic Acid, magyarul politejsav) egy tejsav alapú, biológiailag lebomló műanyag. Általában nádcukrot vagy kukoricakeményítőt erjesztenek bacikkal, ebből lesz a tejsav, amiből észtert varázsolnak, aminek már csak fel kell nyitni a gyűrűjét, hogy polimerizálódjon jól. Igaziból egyszerűbb, ha megveszed egy webshopban a kész drótot, mintha otthon nekiállnál bacikkal büdösíteni némi cukornádat. Amellett, hogy a textilipar PLA szálakat kever a ruhádba, hogy könnyebben vasalható legyen, valamint ebből van a mikrózható műanyag is, a biológiailag lebomló feature miatt egyre inkább használják élelmiszer csomagolóanyagnak (a tetraéder alakú Lipton teafilterek is ebből vannak), illetve ilyen szállal varrják össze a sebed, ha a TB adott pénzt a kórháznak és épp van nekik biológiailag lebomló varratcérnájuk. A biológiai úton történő lebomlása miatt a PLA megkapta a trendi bioplasztik elnevezést is. A PLA 173-178 ℃ között olvad, de egész 110 ℃-ig bírja a hőt. A műanyagipart egybefogó szervezet, az SPI által kitalált Resin ID besorolásban a PLA a 7-es recycling azonosítót kapta:


ABS
Az ABS (Akrinitril-butadién-sztirol) már sokkal ismerősebb anyag lehet – ebből van a LEGO kocka. Ezzel el is mondtam egy csomó tulajdonságát: merev, fényes, deformációnak remekül ellenáll. Hihetetlen módon sztirol és akrinitril polimerizálásával állítják elő… na minek a jelenlétében? Hát még jó, hogy a polibutadién is ott kell, hogy legyen! Az ABS a fröccsöntőipar kedvence. A polibutadién gumi elég szívóssá teszi az amúgy jó szilárdságú akrinitril és sztirol polimereket, szóval klassz kis anyag ez. Az ABS egyedül a tartós UV sugárzást nem szereti, de nekünk nem a szoliba kell, úgyhogy ez nem probléma. Az ABS-t általában petróleumból gyártják – nagyjából 2 kg petróleumból jön össze 1 kg ABS. ABS-t a printerünk 265 ℃-on szereti enni. Sokkal nehezebben tapad, mint az előbb emlegetett PLA, ezért érdemes fűtött platformmal rendelkező nyomtatóval printelni. ABS szálból a PLA-hoz hasonlóan csillióféle szín létezik:

Nylon
A Taulman gyárt nylon alapú, kifejezetten 3D printhez tervezett alapanyagot. A szál piszkosfehér színű, 240-250 ℃ az ajánlott nyomtatási hőfoka, a gyártó a szálat egy henger nélküli tekercsben szállítja, így érdemes a beszerzése előtt rákészülni az új anyagra egy tartóhenger nélküli szálköteg spulni legyártásával.Fának látszó anyag
A LAYWOO-D3 fastruktúrát mintázó alapanyag. Én erre annyira izgulok, mint az autók faberakásaira (=nem), de azért nézzük meg, mert itt a helye az alapanyag postban:Maradékok
Előfordulhat, hogy kisebb-nagyobb száldarabjaid maradnak egy idő után, amiket egyszerűen sajnálnál kidobni. Az ilyen maradékok újrahasznosításához csinált egy ragasztógépet RichRap Thingiverse user. Ezen felül lesz majd egy rakat elrontott print, amit szintén vétek lenne kidobálni, hisz az elérhető árú extruder 3D printerek térnyerésével nagy eséllyel jönnek majd az otthoni recycler eszközök is. Marcus Thymark már neki is állt a dolognak és egy horrorfilmekbre emlékeztető trancsírozógépet tervezett egybe egy húsdaráló-szerű szörnyeteggel (az alábbi videóban 2:00-7:00 között csak különböző recyclable anyagokkal eteti a fémdisznót, szóval azt akár át is ugorhatod): Erre a malacra épülhet aztán a Kickstarteres Filabot:Spéci cuccok
Ha jobban belegondolsz, a 3D nyomtatás anyaga bármi lehetne, ami a nyomtatási eljárás során egymáshoz képes ragadni és nem is deformálódik el túlságosan. Nyomtathatnánk mondjuk… cukorral! Legyen az alapanyag szilárd rúd forma helyett folyékony, a nyomtatófej melegített extruder helyett egy fecskednő és már meg is vagyunk: És ez olyannyira nem távoli cyber dolog, hogy pl. mechadense már össze is rakott ilyen sütiprintert a saját Ultimakeréből. Még mindig van durvább – nézzünk csak meg egy TED előadást, amely arról szól, hogy hogyan nyomtatnak emberi vesét: Ennyi rizsa után ígérem, hogy legközelebb már csinálunk is valami hasznosat. Stay tuned!]]>3D nyomtatás – tuning
Hibásan tervezett/nyomtatott objektum
Mielőtt nekiállnék a gyártót okolni, nézzük meg, mit tudok magamtól tönkretenni. Itt van mindjárt a rosszul megtervezett || nyomtatáshoz rosszul beállított objektum esete. Nézzük csak ezt a kis üreges rudat példának:
A fotón látható téglatest tetejére egy 10 * 4 mm keresztmetszetű, a téglatest hosszában végigfutó üreget kellett tervezni. Mivel a nyomtatáskor az objektum a képen látható módon feküdt a tárgyasztalon, a 10 mm “átfeszítést” helyenként már nem tolerálta jól az olvadt műanyag.
Ezzel két dolgot lehetett tenni: vagy csökkenteni a nyersanyag olvasztási hőmérsékletét, vagy pedig az egész tárgyat állítva nyomtatni, hogy így ne készüljön átfeszített rész egyáltalán.
Summa summarum, ez tehát 100% user error, ami minimális agymunkával és/vagy némi rutinnal már könnyen védhető.
Megszámolható rétegek
A standard Ultimaker extruder fej 0.4 mm átmérőjű – ez elméletileg azt jelentené, hogy a printerrel elérhető nyomtatási pontosság is 0.4 mm lesz. Ez azonban nem teljesen igaz, mivel a léptetőmotorok ettől sokkal pontosabb léptetésre képesek – nézd csak meg pl. Yodát a tárgyasztalon – az alábbi képen a Mester 20 μm rétegvastagsággal készült: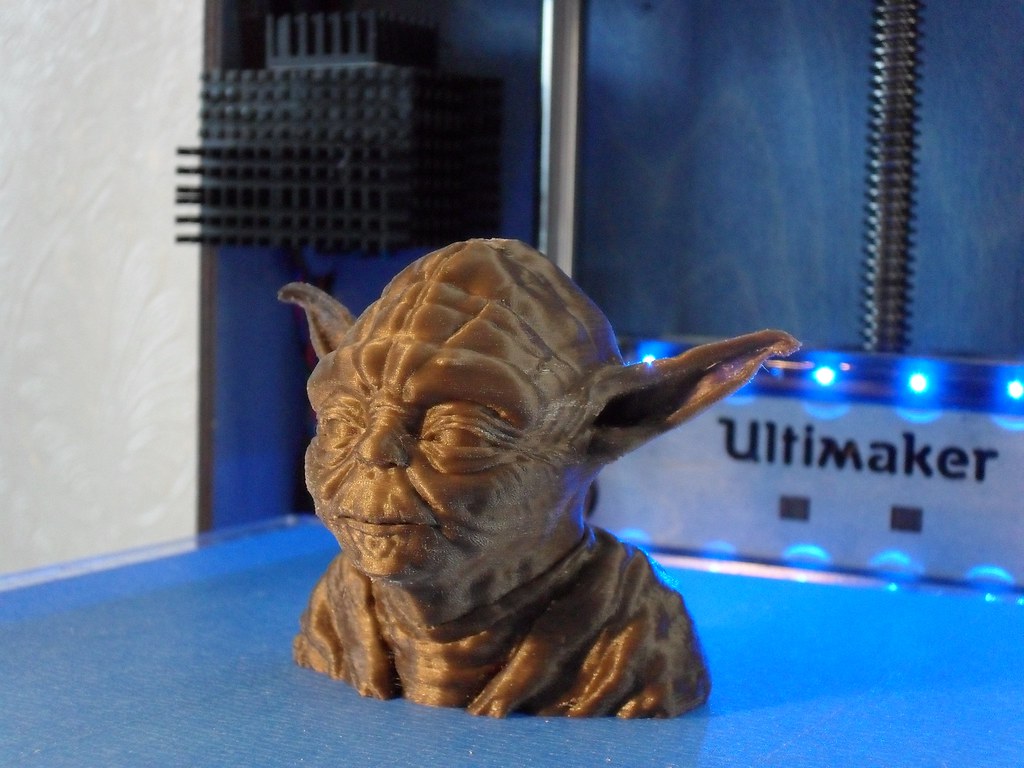
Felesleges szálak, szőrök (=stringing)
Az előző post végén volt erre egy tökéletes példa egy félresikerült GoPro skeleton mount személyében:
- nyersanyag visszahúzatása utazás során a feederrel (=retraction)
- rétegvastagság csökkentése
- hőmérséklet csökkentése
- …vagy simán csak levágod őket egy textilkéssel a print végén, azt Sanyi


Elduguló extruder fej
Szerencsére ez is már csak történelem. A korábban gyártott extruder mechanizmust a megolvasztott nyersanyag képes volt eltömni. A dolog odáig fajult, hogy Ultimakerék külön wiki oldalt szenteltek a duguláselhárításnak, majd kisvártatva előálltak egy új extruder fej design-nel – ezt nevezik Hot end v2-nek. Az új verziónál egy érdekes talpas rézcső csatlakozik a teflon alkatrészbe, amit én az összeszerelésnél azonnal ketté tudtam törni:
Foltosodás (=blobbing)
Én szerencsére nem találkoztam már ezzel a jelenséggel, csak olvastam róla, így a teljesség kedvéért idekerül. A blobbing kis puklik megjelenése a nyomtatott modellen. Ezt korábban az okozta, hogy némelyik printer szoftver/förmver (de ronda ez így magyarul) kombináció nyomtatás közben túl gyorsan pollozta az extruder fej mért hőfokát, amitől az USB “adatcső” be tudott dugulni és csuklott egyet ilyenkor a nyomtatófej. Soros port coder nindzsáknak esetleg ismerős lehet a problémaLazuló hajtószíjak
A nyomtatófejet mozgató tengelyekre a hajtást 2*2 db hosszú gumiszíj adja át. Hosszabb használat után ezek hajlamosak valamennyit megnyúlni, aminek az lesz a következménye, hogy a fej pozícionálása nem lesz olyan precíz, mint azok új korában. Persze a legjobb megoldás az lenne, ha a két servo motor a két tengelypárt valamilyen direktebb kapcsolódással hajtaná meg, de ahhoz sokkal izmosabb módosításra lenne szükség, mint amit az én fakezem elvégezni képes, így fókuszáljunk inkább arra, hogy hogyan tudnánk feszesen tartani a hosszú meghajtószíjakat. A Thingiverse-en a “belt tension” kifejezésre keresve elképesztő mennyiségű övfeszítő változat jön szembe. Én chasmaker megoldását választottam, amely az XY tengelyeken futó vezetőszánokba épül be. Ebben a megoldásban 4 pár, különböző méretű klipszet kapunk, amelyet a hajtószíjak lazaságától függően kell alkalmazni. Hogy melyik pár jó neked, azt egész egyszerűen az dönti el, hogy melyiket tudod pusztán a saját izomerőd felhasználásával még épp beépíteni a szánba. Van erre Ultimakerék szerint precízebb megoldás is, amit én minden további kommentár nélkül csak képzett zongorahangolóknak tudnék ajánlani (először nem hittem el, hogy ezt egy mérnük csapat postolta):Vérbuta papírszerű légterelő cseréje
Ultimakerék az alábbi hajtogatós légterelő megoldást szállítják a nyomtatóval:

Optikai tuning
Na ez az, amit sosem értettem egy autó esetében, itt azonban azonnal rohantam az IKEÁba alkatrészért – nézzük is, hogy miben áll mindez! A 3D nyomtatásban magán a kész produktumon kívül van még két gyerekes öröm. Az egyik, amikor elkészülni látod a “saját gyereked”, a másik pedig az olvadó műanyag szaga (ez utóbbit gondolom mindenki érti, aki szereti a benzin szagát – csak akkor érzed, amikor 3D printelsz, az agyad meg összeköti a két ingert). Van itt egy harmadik mellékhatás is, az pedig a szervómotorok zaja, ami azért inkább bántó, mint izgis. Előbb-utóbb timelapse mozit akarsz csinálni abból, ahogy a fej létrehozza az objetumot a tárgyasztalon – azt pedig mindenki tudja, hogy jó képhez jó fények kellenek. Szerencsére ilyen tuning is van már, nem is egy, konyhakészen. Az első a nyomtató aljába és két oldalsó oszlopába illeszt be egy-egy ledcsíkot. A ledcsíkunk az IKEA konyhakészre gyártott LEDBERG ledcsíkja, az ehhez való kompatibilis illesztést pedig mpatoulachik készítette a Thingiverse közösség számára.

Fűtött tárgyasztal
Ez még egy érdekes fejlesztési pont. Ultimakerék egyelőre hivatalosan nem kínálnak fűtött tárgyasztalt (=heated bed) a nyomtatójukhoz. A fűtött tárgyasztal legfőbb előnye, hogy a melegen tartott üveg vagy alumímium felületen sokkal jobban tapad a nyersanyag, így stabilabban áll rajta a létrehozott modell, valamint szükségtelenné válik az akril lapot védő ragasztócsíkok használata. Sok próbálkozás létezik már, a Prusa Mendel féle printerekhez pl. már kapható is megfelelő fűtőbetét, de ezek nekem még nem kiforrottak. A modderek egy része arra esküszik, hogy a fűtőbetétet üveglap alá kell pakolni, míg másik részük arra, hogy egy teljesen sík 6 mm-es vastagságú alumínium lemez a jó megoldás, lévén az sokkal jobb hővezető (nota bene: a heated bed platformról csak a platform kihűlése után távolítható el a kész objektum, mí az akril asztalnál azonnal szedheted le a cuccot). Már a tárgyasztal egyenletessége is kemény dió, tekintve, hogy itt 0.05 mm eltérés is okozhat problémákat a nyomtatásnál. Az üveg tárgyasztal tuningok sem akármilyen síküvegből készülnek, szinte mindenki boroszilikátot használ. Alumínium esetén pedig 6 mm vastagságú, 20×20 cm-es, teljesen sík lemezt beszerezni megint csak nem kis kihívás. E mellé érkezik még a fűtőszál feszültséggel való ellátásának gondja is. Ha ugyanis gyengeárammal szeretnénk tolni a fűtőlemezt, akkor ahhoz minimum 300-400 Wattos, vaddisznó méretű PC-like tápra van szükség, ha viszont mindezt erősárammal oldanánk meg, azzal pedig beköltöztetjük a birkózógépet a nyomtatónkba, ami jól megölheti az ügyetlen tuningolót. Summa summarum, nekem ez még nem kell, dolgozzanak csak még rajta a mérnökök.Speedy Gonzales
Beszélnünk kellene még egy kicsit a sebesség kérdéséről is, de én ebben (is) nagyon amatőr vagyok még. Ha az olvasott emlékeim nem csalnak, akkor a Marlin firmware-ek valahol 160 mm/sec környékére limitálják a a fejmozgatás max. sebességét. Ezzel persze bárki szabadon játszhat annak érdekében, hogy gyorsítson a nyomtatási sebességen, sokat ártani nem tudunk, maximum nem lesz jó a print. Azt is figyelembe kell venni a fejmozgatási sebesség piszkálásakor, hogy a nyersanyag hőfoka, a rétegvastagság és a fej mozgási sebessége három, egymással összefüggő paraméter, így a másik kettőt is érdemes utánhúzni. Nekem egyelőre jó a default is.Kalibráló nyomtatás
Miután átesünk egy-egy tuninglépésen, érdemes ellenőrizni, hogy a printerünk minden szempontból precízen teszi-e a dolgát. Erre találta ki 3dprinterbot az átlátszó kalibrációs piramist. Ezt letöltjük, kinyomtatjuk és ha nagyjából egy precíz objektumot kapunk, akkor már nagy gáz nem lehet:
3D nyomtatás – a buktatók
szebbnél szebb printet, látja az eszement sebességgel dolgozó nyomtató robotokat, majd úgy gondolja, hogy ez neki is azonnal ugyanúgy menni fog. Hát nem.
Kezdésnek tekintsük át a 3 dimenziós nyomtatás munkafolyamatát. Ehhez ellopjuk Florian Horsch blogjáról az általa készített remek összefoglaló ábrát:
Szóval nem csak úgy megy, hogy letöltök egy objektumot, aztán megnyomom a print gombot.
Szerezzünk modellt
Persze azonnal alkotni is lehet valami 3D tervező szoftverrel, de tegyük fel, hogy túl éhesek vagyunk és azonnal kellene valami nyomtatnivaló. Ez esetben menjünk el mondjuk a thingiverse.com-ra és töltsünk le egy szívünknek kedves ojjektumot, STL formátumban.A modell előkészítése
Definiálnunk kell a célobjektum méretét, valamint azt is, hogy melyik irányban álljon nyomtatáskor az objektum a tárgyasztalon. Szükség lehet alapvető optimalizálási műveletek elvégzésére is, mint mondjuk a lyukas objektumok bezárása. Ráadásul nem minden tárgy nyomtatható az extruder eljárással – gondoljunk csak arra, hogy egy levegőben lógó részt hogyan alakítana ki a nyomtatófej, mihez ragasztaná a kilógó darab első rétegét? Nézzük csak meg ennek a kis mukinak a kezeit pl:
Szeletelés
Ha az első fázison túl vagyunk és előállt egy hibamentes modell, amit nyomtatnánk, akkor jöhet a szeletelés (=slicing). Mivel a printerünk rétegeket nyomtat, ezért nekünk a modellünket ugyanígy rétegekre kell bontanunk:
- beletöltjük az előbb már emlegetett STL formátumba kimentett objektumunkat (az STL a CAD/CAM rendszerek kedvenc közös 3D objektumformátuma)
- elhelyezzük azt a tárgyasztalon
- nyomtatáshoz optimális irányba forgatjuk
- beállítjuk a méretét
- …majd definiáljuk még:
- a rétegvastagságot
- a falvastagságot
- a kezdő és záró réteg vastagságát
- az objektum belsejének kitöltöttségét
- a nyomtatási sebességet
- a nyomtatófej nyersanyagtól függő nyomtatási hőmérsékletét
- a nyersanyag átmérőjét
- a nyomtatás előtt opcionálisan húzandó “szoknya” vonalszámát és tárgytávolságát
- a szintén opcionális támasztékot
Végre nyomtatunk?
Ahhoz, hogy nyomtatni tudjunk, a nyomtató alkalmazásnak a gépünk USB portjára csimpaszkodó nyomtatóval kell tudnia beszélgetni. A beszélgetés kétirányú kell, hogy legyen, hiszen addig az eszközünk nem kaphat pl. nyomtatási parancsot, amíg az extruder fej hőfoka nem megfelelő. Gondolj csak bele, mi lesz abból, ha elkezdjük tolni az etető mechanizmussal a műanyag szálat a még hideg fejbe! A beszélgetéshez a nyomtató agyába is kell egy protokoll. Az Ultimaker agya per pillanat egy Arduino Mega 2560. Az agyban levő firmware-t nálam Marlinnak hívják, de ebből is van jó sok féle, hogy kicsit tovább bonyolódjon a helyzet. Mindenesetre Curát választva a Cura szépen felpakolja a számára szimpatikus Marlin release-t, mi több, gondoskodik az esetleges frissítésekről is. Tegyük fel ott tartunk, hogy megvan az objektumunk, az fel van szeletelve GCODE formátumban (vagy esetleg eleve GCODE formában kaptuk az objektumot), a nyomtató vezérlő alkalmazásunk megfelelően fel van paraméterezve, az elkészült GCODE pedig 100%-ig kompatibilis a nyomtatónk agyában levő protokoll handlerrel. Most már csak ott tartunk, hogy megnyomjuk a printet és kijön a modell élőben, ugye? Nem.Ellenőrizzük a printert
A printer ellenőrzése az a szelet, amit viszonylag kevés helyen olvastam, pedig van annyira fontos, mint az összes előző fázis együttvéve. Nézzünk egy listát, hogy miket kell nyomtatás előtt megvizsgálnunk:Tárgyasztal szintbe állítása
A tárgyasztalunknak és a nyomtatófejünknek tizedmilliméter precizitással kell egymáshoz illeszkednie. Ez nem feltétlenül azt jelenti, hogy a tárgyasztalnak vízszintesnek kell lennie, mivel az korántsem biztos, hogy a nyomtatófejünk teljesen vízszintes síkon szánkázik. Az Ultimaker tárgyasztalát 4 csavar tartja, az asztal rugós lábakon áll. A csavarok tekerésével szabályozható az asztal 4 pontjának magassága. A tárgyasztalt nulla magasságba állítod, a nyomtatófejet kihúzod az egyik sarokba, majd a fej és az asztal közé betolsz egy vékony kartonlapot (én 0.2 mm-est használok). Addig állítasz a legközelebbi csavaron, amíg a kartonlap épphogy kicsit karcolva hagyja csak el az asztal és a fej közti rést. Ezután fej a következő sarokba és ismételsz, míg így mind a négy sarkot be nem lövöd.Feeder (=etető) ellenőrzése
Nyomtatás előtt kiveszed a feeder mechanizmus rovátkolt továbbító tengelyét és lepucolod róla a dzsuvát. Ugyanígy teszel a feeder tengelyének kimart lyukkal is. Ha ezt elmulasztod, majd akkor fogod bánni, ha egy hosszú nyomtatás közepén a feeder nem egyenletesen továbbítja az alapanyagot és a nyomtatott objektumon egyfajta “szőrös” felület jelenik meg az anyaghiány következményeként:
Tárgyasztal zsírtalanítás
Tiszta szesz vagy aceton (=1-3 dimetil keton, amit körömlakk lemosó néven kapsz, az nem biztos, hogy jó, próbáld ki egy kis darabon, hogy nem mar-e) egy papírzsebkendőre, azzal picit áttörlöd a tárgyasztalt és kész. Ha az asztal túl zsíros, nem fog kellően odaragadni az első (és egyben legfontosabb) réteg, és már buktuk is a printet. Az is megoldás, ha minden nyomtatás előtt cseréled a tárgyasztalra ragaszotott védőréteget – apropó védőréteg! Ultimakerék a 3M Scotch Blue tape-et ajánlják ehhez, nekem azonban három problémám is akadt vele. Először is baromi macerás a vékony csíkokat mindig újraragasztani (=9 csík fedi le a tárgyasztalt, ha jól emlékszem), azután se otthon, se itt Krakkóban nem találtam forgalmazót, végül pedig szemérmetlenül drága (=9 EUR egy tekercs). Nem keveset kísérleteztem, sasoltam a barkácsboltokat, míg végül arra jutottam, hogy a festők által az ablakszélek védelmére használt 50 mm széles ragszalag tökéletes ugyanerre a célra, kapható bárhol és a blue tape-hez képest filléres tétel:
Hurrá, nyomtatunk!
Ha mindez kész, mehet a print. Nem mondom, hogy tuti biztos azonnal szuper lesz, de már valamit dob majd a gép: