Hibásan tervezett/nyomtatott objektum
Mielőtt nekiállnék a gyártót okolni, nézzük meg, mit tudok magamtól tönkretenni. Itt van mindjárt a rosszul megtervezett || nyomtatáshoz rosszul beállított objektum esete. Nézzük csak ezt a kis üreges rudat példának:
A fotón látható téglatest tetejére egy 10 * 4 mm keresztmetszetű, a téglatest hosszában végigfutó üreget kellett tervezni. Mivel a nyomtatáskor az objektum a képen látható módon feküdt a tárgyasztalon, a 10 mm “átfeszítést” helyenként már nem tolerálta jól az olvadt műanyag.
Ezzel két dolgot lehetett tenni: vagy csökkenteni a nyersanyag olvasztási hőmérsékletét, vagy pedig az egész tárgyat állítva nyomtatni, hogy így ne készüljön átfeszített rész egyáltalán.
Summa summarum, ez tehát 100% user error, ami minimális agymunkával és/vagy némi rutinnal már könnyen védhető.
Megszámolható rétegek
A standard Ultimaker extruder fej 0.4 mm átmérőjű – ez elméletileg azt jelentené, hogy a printerrel elérhető nyomtatási pontosság is 0.4 mm lesz. Ez azonban nem teljesen igaz, mivel a léptetőmotorok ettől sokkal pontosabb léptetésre képesek – nézd csak meg pl. Yodát a tárgyasztalon – az alábbi képen a Mester 20 μm rétegvastagsággal készült: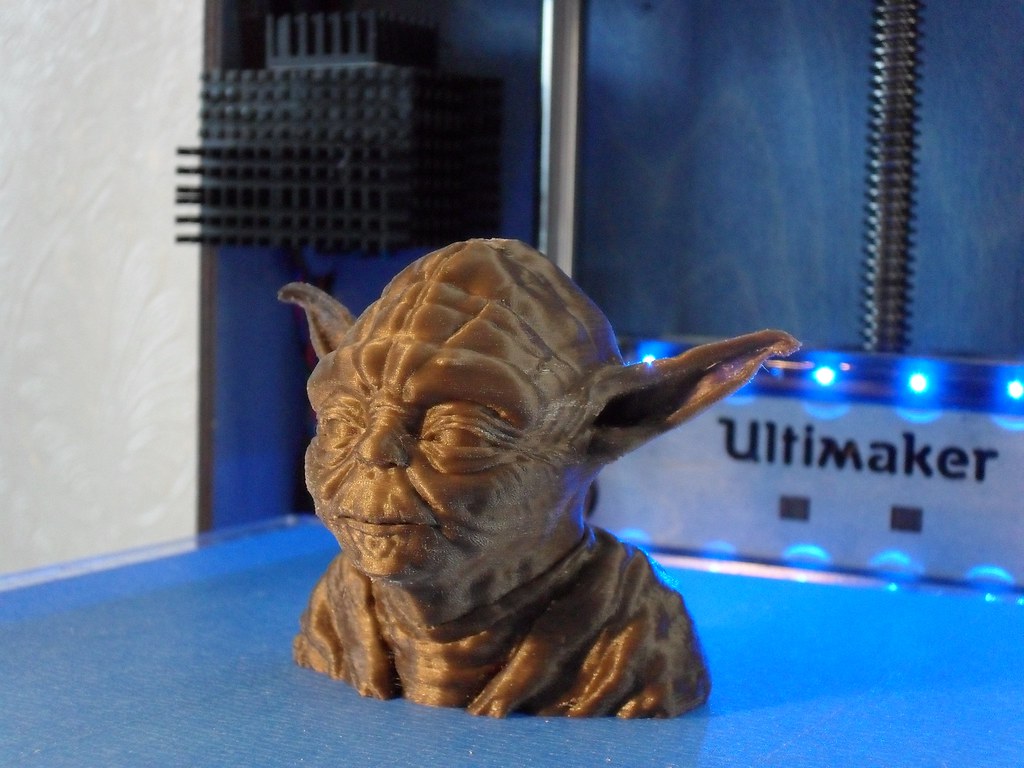
Felesleges szálak, szőrök (=stringing)
Az előző post végén volt erre egy tökéletes példa egy félresikerült GoPro skeleton mount személyében:
- nyersanyag visszahúzatása utazás során a feederrel (=retraction)
- rétegvastagság csökkentése
- hőmérséklet csökkentése
- …vagy simán csak levágod őket egy textilkéssel a print végén, azt Sanyi


Elduguló extruder fej
Szerencsére ez is már csak történelem. A korábban gyártott extruder mechanizmust a megolvasztott nyersanyag képes volt eltömni. A dolog odáig fajult, hogy Ultimakerék külön wiki oldalt szenteltek a duguláselhárításnak, majd kisvártatva előálltak egy új extruder fej design-nel – ezt nevezik Hot end v2-nek. Az új verziónál egy érdekes talpas rézcső csatlakozik a teflon alkatrészbe, amit én az összeszerelésnél azonnal ketté tudtam törni:
Foltosodás (=blobbing)
Én szerencsére nem találkoztam már ezzel a jelenséggel, csak olvastam róla, így a teljesség kedvéért idekerül. A blobbing kis puklik megjelenése a nyomtatott modellen. Ezt korábban az okozta, hogy némelyik printer szoftver/förmver (de ronda ez így magyarul) kombináció nyomtatás közben túl gyorsan pollozta az extruder fej mért hőfokát, amitől az USB “adatcső” be tudott dugulni és csuklott egyet ilyenkor a nyomtatófej. Soros port coder nindzsáknak esetleg ismerős lehet a probléma 🙂 Ezeknél az alkalmazásoknál (úgy emlékszem, a ReplicatorG valamelyik verziója bugzott így) elég volt az is, ha a nyomtatást monitorozó ablakot becsukta az user és így már nem mentek ki a hőmérő pollozó parancsok.Lazuló hajtószíjak
A nyomtatófejet mozgató tengelyekre a hajtást 2*2 db hosszú gumiszíj adja át. Hosszabb használat után ezek hajlamosak valamennyit megnyúlni, aminek az lesz a következménye, hogy a fej pozícionálása nem lesz olyan precíz, mint azok új korában. Persze a legjobb megoldás az lenne, ha a két servo motor a két tengelypárt valamilyen direktebb kapcsolódással hajtaná meg, de ahhoz sokkal izmosabb módosításra lenne szükség, mint amit az én fakezem elvégezni képes, így fókuszáljunk inkább arra, hogy hogyan tudnánk feszesen tartani a hosszú meghajtószíjakat. A Thingiverse-en a “belt tension” kifejezésre keresve elképesztő mennyiségű övfeszítő változat jön szembe. Én chasmaker megoldását választottam, amely az XY tengelyeken futó vezetőszánokba épül be. Ebben a megoldásban 4 pár, különböző méretű klipszet kapunk, amelyet a hajtószíjak lazaságától függően kell alkalmazni. Hogy melyik pár jó neked, azt egész egyszerűen az dönti el, hogy melyiket tudod pusztán a saját izomerőd felhasználásával még épp beépíteni a szánba. Van erre Ultimakerék szerint precízebb megoldás is, amit én minden további kommentár nélkül csak képzett zongorahangolóknak tudnék ajánlani (először nem hittem el, hogy ezt egy mérnük csapat postolta):Vérbuta papírszerű légterelő cseréje
Ultimakerék az alábbi hajtogatós légterelő megoldást szállítják a nyomtatóval:

Optikai tuning
Na ez az, amit sosem értettem egy autó esetében, itt azonban azonnal rohantam az IKEÁba alkatrészért – nézzük is, hogy miben áll mindez! A 3D nyomtatásban magán a kész produktumon kívül van még két gyerekes öröm. Az egyik, amikor elkészülni látod a “saját gyereked”, a másik pedig az olvadó műanyag szaga (ez utóbbit gondolom mindenki érti, aki szereti a benzin szagát – csak akkor érzed, amikor 3D printelsz, az agyad meg összeköti a két ingert). Van itt egy harmadik mellékhatás is, az pedig a szervómotorok zaja, ami azért inkább bántó, mint izgis. Előbb-utóbb timelapse mozit akarsz csinálni abból, ahogy a fej létrehozza az objetumot a tárgyasztalon – azt pedig mindenki tudja, hogy jó képhez jó fények kellenek. Szerencsére ilyen tuning is van már, nem is egy, konyhakészen. Az első a nyomtató aljába és két oldalsó oszlopába illeszt be egy-egy ledcsíkot. A ledcsíkunk az IKEA konyhakészre gyártott LEDBERG ledcsíkja, az ehhez való kompatibilis illesztést pedig mpatoulachik készítette a Thingiverse közösség számára.

Fűtött tárgyasztal
Ez még egy érdekes fejlesztési pont. Ultimakerék egyelőre hivatalosan nem kínálnak fűtött tárgyasztalt (=heated bed) a nyomtatójukhoz. A fűtött tárgyasztal legfőbb előnye, hogy a melegen tartott üveg vagy alumímium felületen sokkal jobban tapad a nyersanyag, így stabilabban áll rajta a létrehozott modell, valamint szükségtelenné válik az akril lapot védő ragasztócsíkok használata. Sok próbálkozás létezik már, a Prusa Mendel féle printerekhez pl. már kapható is megfelelő fűtőbetét, de ezek nekem még nem kiforrottak. A modderek egy része arra esküszik, hogy a fűtőbetétet üveglap alá kell pakolni, míg másik részük arra, hogy egy teljesen sík 6 mm-es vastagságú alumínium lemez a jó megoldás, lévén az sokkal jobb hővezető (nota bene: a heated bed platformról csak a platform kihűlése után távolítható el a kész objektum, mí az akril asztalnál azonnal szedheted le a cuccot). Már a tárgyasztal egyenletessége is kemény dió, tekintve, hogy itt 0.05 mm eltérés is okozhat problémákat a nyomtatásnál. Az üveg tárgyasztal tuningok sem akármilyen síküvegből készülnek, szinte mindenki boroszilikátot használ. Alumínium esetén pedig 6 mm vastagságú, 20×20 cm-es, teljesen sík lemezt beszerezni megint csak nem kis kihívás. E mellé érkezik még a fűtőszál feszültséggel való ellátásának gondja is. Ha ugyanis gyengeárammal szeretnénk tolni a fűtőlemezt, akkor ahhoz minimum 300-400 Wattos, vaddisznó méretű PC-like tápra van szükség, ha viszont mindezt erősárammal oldanánk meg, azzal pedig beköltöztetjük a birkózógépet a nyomtatónkba, ami jól megölheti az ügyetlen tuningolót. Summa summarum, nekem ez még nem kell, dolgozzanak csak még rajta a mérnökök.Speedy Gonzales
Beszélnünk kellene még egy kicsit a sebesség kérdéséről is, de én ebben (is) nagyon amatőr vagyok még. Ha az olvasott emlékeim nem csalnak, akkor a Marlin firmware-ek valahol 160 mm/sec környékére limitálják a a fejmozgatás max. sebességét. Ezzel persze bárki szabadon játszhat annak érdekében, hogy gyorsítson a nyomtatási sebességen, sokat ártani nem tudunk, maximum nem lesz jó a print. Azt is figyelembe kell venni a fejmozgatási sebesség piszkálásakor, hogy a nyersanyag hőfoka, a rétegvastagság és a fej mozgási sebessége három, egymással összefüggő paraméter, így a másik kettőt is érdemes utánhúzni. Nekem egyelőre jó a default is.Kalibráló nyomtatás
Miután átesünk egy-egy tuninglépésen, érdemes ellenőrizni, hogy a printerünk minden szempontból precízen teszi-e a dolgát. Erre találta ki 3dprinterbot az átlátszó kalibrációs piramist. Ezt letöltjük, kinyomtatjuk és ha nagyjából egy precíz objektumot kapunk, akkor már nagy gáz nem lehet:
Pingback: 3D nyomtatas – iPhone5 autós dokkoló « eFi.blog
Pingback: 3D nyomtatás – tuning v2 « eFi.blog
Pingback: Kalandozásaink a 3D nyomtatás földjén | APPSolute